Laser cleaning has revolutionized the way we approach the maintenance and restoration of steel structures and components. By harnessing the power of laser technology, industries are able to achieve a level of cleanliness and precision that was previously unattainable. This method is not only effective for large-scale operations but also for detailed work on delicate parts.
Laser cleaning is a non-contact, environmentally-friendly, and highly precise method for removing unwanted substances from steel surfaces. In this article, we’ll delve into the benefits and process of laser cleaning for steel surfaces, examining how it compares to traditional methods and exploring the future of this innovative technology.
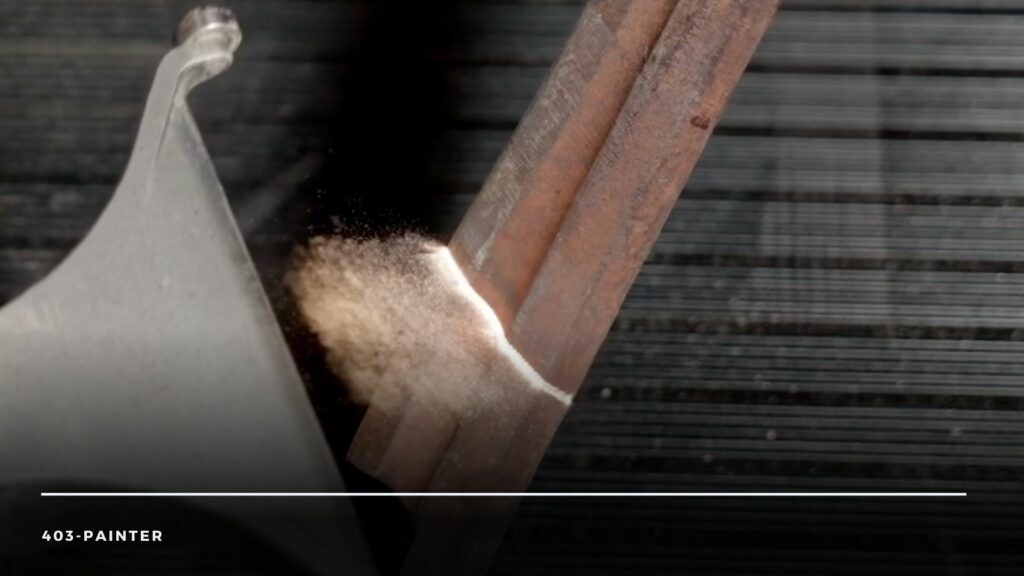
What is Laser Cleaning?
Laser cleaning is a non-abrasive surface cleaning process that uses high-intensity laser beams to remove unwanted substances from a surface. This process is ideal for removing rust, paint, and other contaminants from steel surfaces without damaging the material. The laser beam vaporizes the unwanted substance, leaving behind a clean and undamaged surface.
Compared to manual scrubbing or harsh chemical applications, laser cleaning offers a much more refined approach. It is designed to target only the unwanted layers, preserving the integrity of the underlying steel. This selective removal is not just effective for cleaning; it is also an excellent way to restore historical artifacts or machinery where maintaining the original material is crucial.
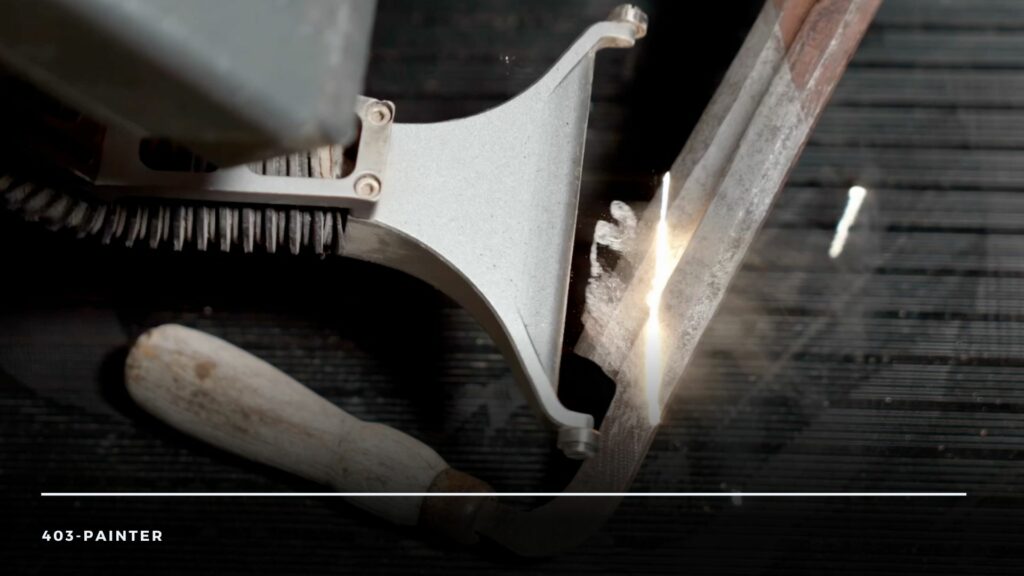
The Advantages of Laser Cleaning
Environmentally-Friendly
Unlike traditional methods, laser cleaning does not involve the use of chemicals or abrasive materials. This makes it an eco-friendly method for surface cleaning, as there is no hazardous waste produced in the process. Additionally, the laser beam does not produce any harmful fumes or emissions, making it safe for both the environment and the operators.
The absence of chemicals also eliminates the need for disposal of toxic materials, which can be both costly and challenging from a regulatory standpoint. With laser cleaning, the only byproduct is the vaporized residue from the contaminants, which can often be collected and disposed of with ease.
Cost-Effective
Laser cleaning is a cost-effective solution for steel surface cleaning. While traditional methods may require the use of chemicals, sandblasting equipment, or replacement parts, laser cleaning only requires the use of the laser and minimal maintenance. This means lower costs for materials and maintenance, as well as increased productivity due to the quick and efficient cleaning process.
The reduction in downtime is another factor that contributes to the cost-effectiveness of laser cleaning. Since laser cleaning is a dry process, there is no need for drying time, which means that parts and structures can be returned to service almost immediately after cleaning. This increased turnaround time is invaluable for industries where equipment uptime is critical.
Precision Cleaning
Laser cleaning is a highly precise method for removing unwanted substances from steel surfaces. The laser beam can be adjusted to a specific size and intensity, allowing for spot cleaning and the removal of even the smallest particles. This makes it an ideal solution for precision cleaning in industries such as aerospace, automotive, and electronics.
In applications that require a high degree of accuracy, such as the aerospace industry, the precision of laser cleaning is unmatched. It allows for the selective removal of coatings or contaminants without affecting the intricate engineering beneath. This level of control is essential for maintaining the functional and structural integrity of critical components.
Safe and Versatile
The laser cleaning process is non-contact, meaning the laser beam does not physically touch the surface being cleaned. This makes it a safe method for cleaning delicate or intricate parts without causing any damage. Additionally, the laser beam can be used on various types of steel surfaces, including flat, curved, and irregular shapes, making it a versatile solution for different industries.
Safety is significantly enhanced with laser cleaning, as it reduces the risk of accidents associated with manual cleaning or the use of hazardous substances. The versatility of the laser extends its application beyond steel to a variety of materials such as aluminum, titanium, and even some plastics, making it an indispensable tool in a diverse range of applications.
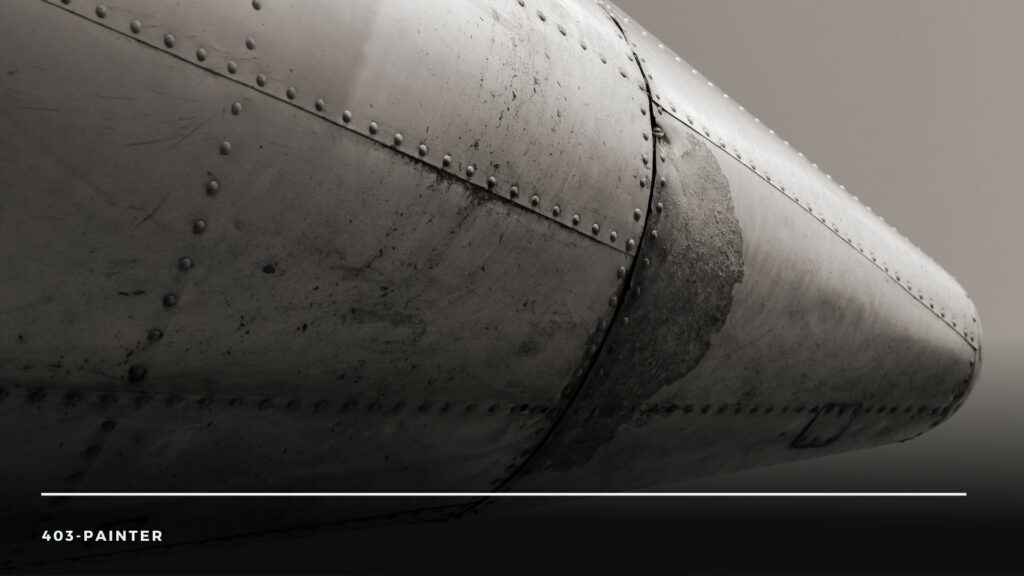
The Industrial Laser Cleaning Process
The laser cleaning process involves the use of a high-intensity laser beam to remove unwanted substances from steel surfaces. Here are the steps involved in the process:
Step 1: Preparation
Before the laser cleaning process can begin, the surface to be cleaned must be prepared. This involves removing any loose debris or large particles that may interfere with the laser beam. Additionally, safety measures must be taken to protect operators and bystanders from the laser beam.
Proper preparation also includes ensuring that the laser equipment is calibrated and functioning correctly. The work area must be secured, and, if necessary, barriers or protective screens are set up to contain the laser operation. This step is vital for the safety of everyone in the vicinity and for the efficiency of the cleaning process.
Step 2: Adjusting the Laser Beam
The laser beam is then adjusted to the desired size and intensity for the specific cleaning task. This is important for precision cleaning, as it ensures that only the unwanted substance is removed, leaving the surface undamaged.
Fine-tuning the laser parameters is a critical aspect of the cleaning process. It requires skilled operators who understand the interaction between the laser and different types of contaminants or coatings. The ability to adjust the laser on-the-fly allows for adaptability when tackling complex or varied cleaning tasks.
Step 3: Cleaning
The laser beam is then directed towards the surface to be cleaned. As the laser beam makes contact with the unwanted substance, it heats it up and vaporizes it, leaving behind a clean surface. The laser beam can be moved along the surface in a sweeping motion, allowing for efficient and thorough cleaning.
The cleaning phase is where the laser truly shines. The precision of the laser means that it can be used for detailed work, such as cleaning the intricate parts of machinery or removing specific layers of paint or corrosion without damaging the underlying material. This targeted approach minimizes waste and maximizes the effectiveness of the cleaning process.
Step 4: Removal of Residue
Once the cleaning process is complete, any residue or vaporized particles are removed from the surface using a vacuum or compressed air. This ensures that the surface is completely clean and ready for further processing or use.
The final step is crucial to ensure the cleanliness of the surface. The removed particles must be carefully collected to prevent any possible contamination. This step often involves the use of specialized filtration systems to capture the fine particles and dispose of them in an environmentally responsible manner.
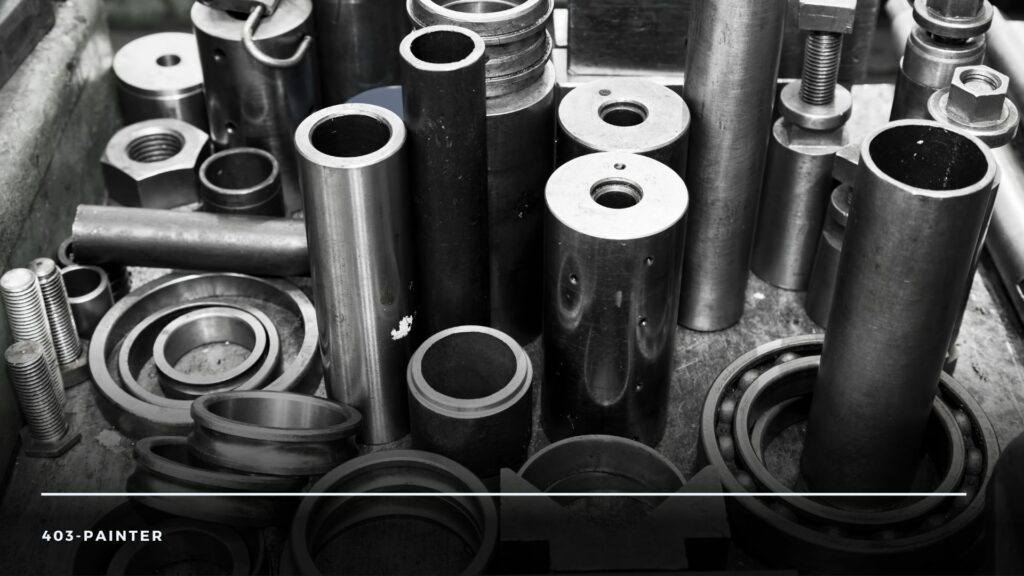
Applications of Industrial Laser Cleaning
Laser cleaning has a wide range of applications in different industries. Here are some of the common uses of laser cleaning for steel surfaces:
Rust Removal
Laser cleaning is an effective method for removing rust from steel surfaces without damaging the material. This is particularly useful for restoring old machinery or equipment.
Paint Removal
Laser cleaning can remove paint from steel surfaces without damaging the material. This is useful for repainting or refinishing steel parts or structures.
Contaminant Removal
Laser cleaning can remove contaminants such as oil, grease, and dirt from steel surfaces, ensuring the surface is clean and ready for use.
Surface Preparation
Laser cleaning can be used as a surface preparation method for painting, coating, or welding. The laser beam removes any unwanted substances, leaving behind a clean and smooth surface for further processing.
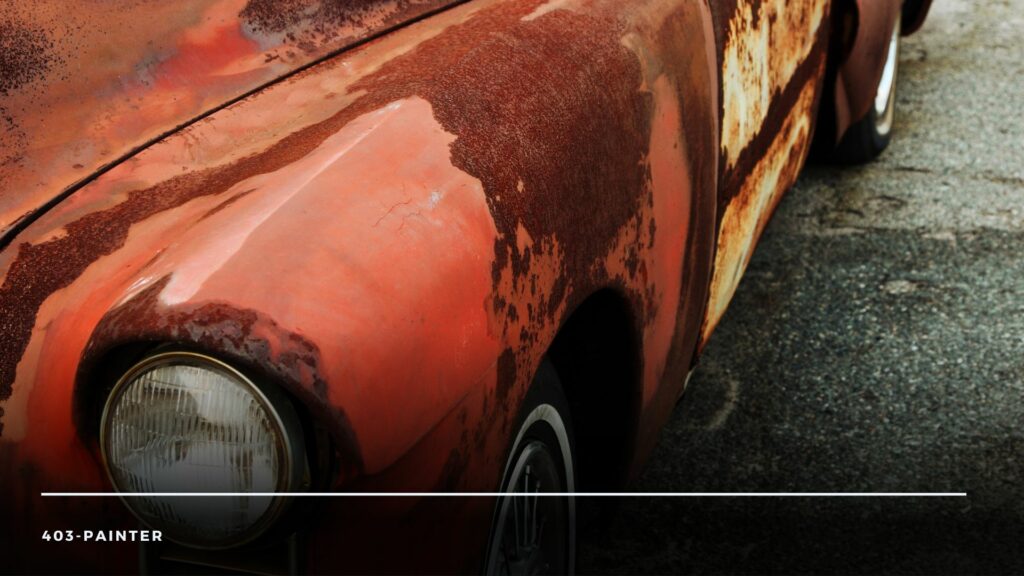
The applications of laser cleaning are not limited to the examples mentioned above. It is also employed in conservation work to restore historical monuments and artifacts, in the medical industry for the sterilization of surgical equipment, and even in the energy sector for the maintenance of power generation equipment. The versatility and effectiveness of laser cleaning make it a sought-after solution across a broad spectrum of sectors.
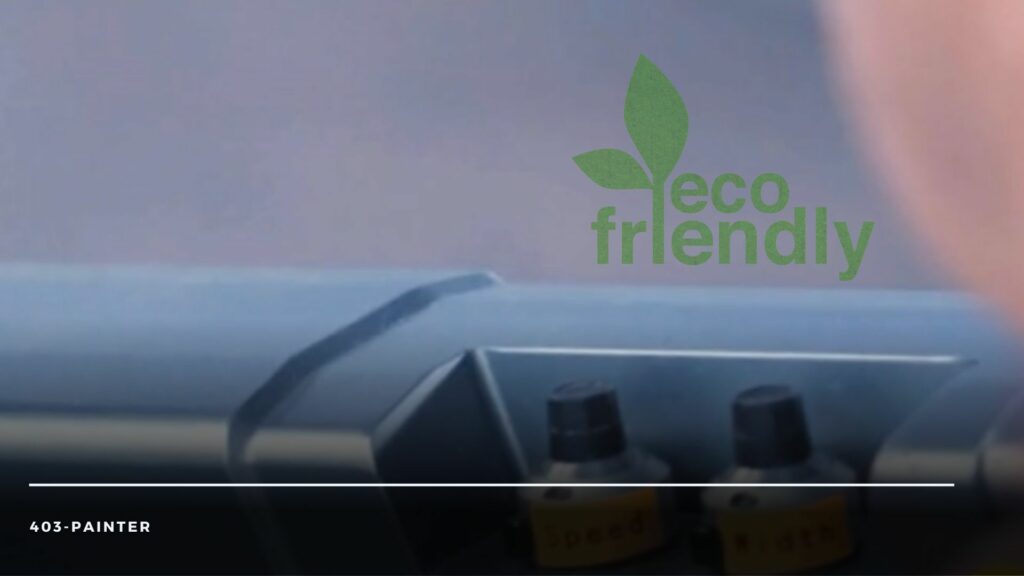
The Future of Laser Cleaning for Steel Surfaces
With the increasing demand for more efficient, cost-effective, and environmentally-friendly cleaning methods, the use of laser cleaning is expected to grow in the coming years. The advancements in laser technology have made it possible to use laser cleaning for larger surface areas, making it a viable solution for industrial cleaning.
Furthermore, as we push the boundaries of what’s possible with laser technology, we’re finding new and innovative ways to integrate it into various manufacturing and maintenance processes. The potential for laser cleaning to be combined with other technologies such as 3D scanning and artificial intelligence could lead to even more precise and autonomous cleaning systems.
Additionally, the use of robotics and automation in laser cleaning is becoming more prevalent, making it a safer and more efficient process. This allows for the cleaning of hard-to-reach or hazardous areas without putting operators at risk.
The integration of laser cleaning into automated and robotic systems not only enhances safety but also significantly increases efficiency. Robots can be programmed to perform repetitive and precise cleaning tasks with little to no human intervention, which is especially beneficial in hazardous or difficult-to-access environments.
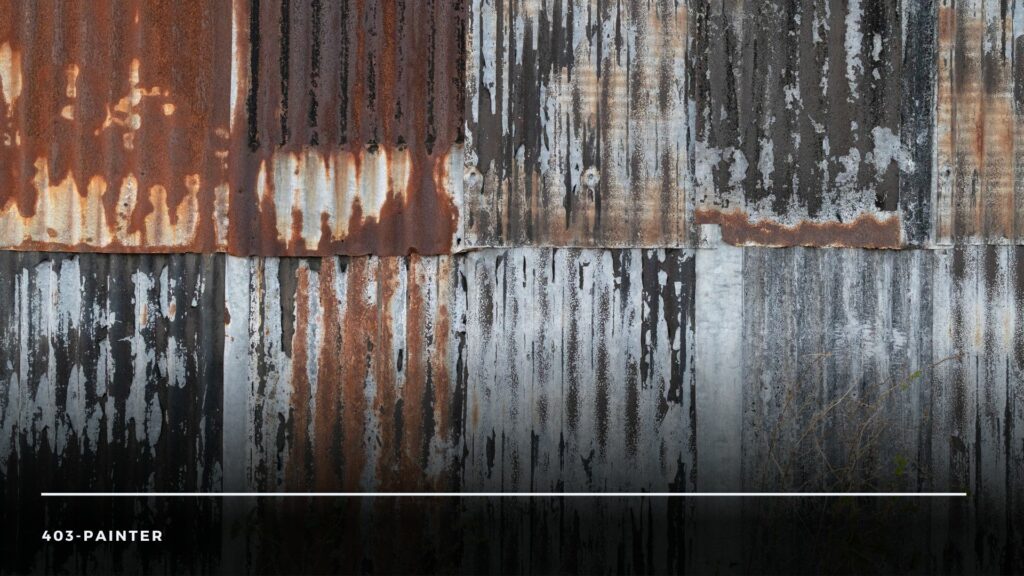
Why You Should Consider Laser Cleaning
Laser cleaning is a highly efficient, precise, and environmentally-friendly method for removing unwanted substances from steel surfaces. Its benefits, such as cost-effectiveness, precision cleaning, and versatility, make it a popular choice in various industries. As technology continues to advance, the use of laser cleaning is expected to grow, making it an essential tool for surface cleaning and preparation.
The future of laser cleaning looks bright, with continuous improvements in laser power, efficiency, and control. It is poised to become an even more integral part of industrial processes, contributing to a cleaner, safer, and more sustainable world.